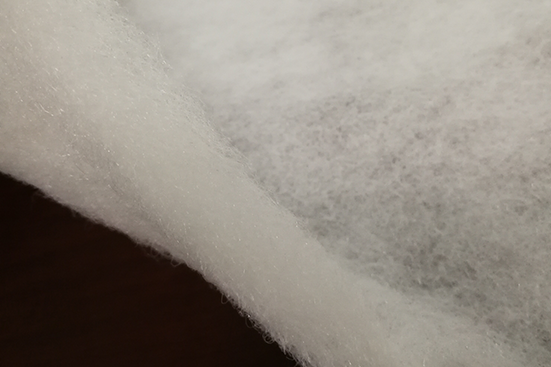
Blended cotton-opening-secondary opening-mixing cotton
box-carding-laying-hot air setting-cooling-cutting curling
1. Blending cotton: According to the different requirements of customers,
we need to match the fiber cotton of different proportions according to
different proportions. After weigh the initial weight, we pour the mixer into
the mixer and stir it by machine. The purpose is to stir all kinds of raw
materials evenly.
2. Opening the pine: the agglomerated fiber will be transferred to the
licker device through the roller, and then the fiber bundle will be opened in a
continuous manner, and then the fiber bundle will be sent to the second opening
by the fan. Send the device. After the fiber bundle is sent twice, it is sent to
the mixing box by the fan, and mixed by the vibration of the bucket.
3, combing: Xilin and Doffer comb the car industry inside the thickness of
the uniform, evenly distributed cotton layer transferred to the upper screen,
and then spread the screen into a net.
4, paving the net: swinging back and forth by the shake screen, paved into
a uniform mesh layer and then sent to the oven from the bottom screen.
5, hot air shaping: the uniform cotton layer is sent to the oven, the low
melting point fiber in the oven at a certain temperature will hold together the
various fibers to form synthetic fiber cotton.
6. Cold air shaping and trimming curling: After the synthetic cotton fiber
is shaped by cold air, the thickness is determined by the pressing shaft, and
then the trimming edge of the specified value is passed. When the length reaches
the specified value, it is cut by the thermal fuse and then rolled.